"Innovation. Precision. Automation. Welcome to CAPL, where technology meets excellence."
SEMI AUTOMATIC ARCH CHAMBER ASSEMBLY MACHINE

Key features of CAPL Arc chamber assembly machine
1. Very less power consumption (Single Phase @ < 1 KW)
2. Runs only in Electric + Pneumatic Energy
3. Assembly speed of 60 parts per minute (*)
4. Inbuilt heaters to soften fiber paper before stamping
5. Traction of 350N possible with 6 bar air pressure
6. In-built Pressure sensor to stop machine if pressure falls
7. Intelligent Tool life warning system
8. Inbuilt Mechanical Press for making V notches for more traction
9. All pneumatic elements from SMC
10. HMI and PLC from Mitsubishi
11. Local hardened inserts used for all wear locations
12. Chrome and Nickel plated machine elements
13. Very easy to operate HMI layout.
14. Pictorial display of all sensor’s position
15. Inbuilt sensors insure that machine stops if any arc plate or fiber is missing
16. Very fast vibro feeder which can feed sufficient arc plates even if machine runs at 80 SPM
17. All four tracks of feeder can be fed in less than 2 minutes
18. All-important vibro feeder elements made with stainless Steel
19. Ejection station has dedicated ejector pins for all plates so it ensures ejection of everything even if fiber paper is missing.
20. Password protected HMI ensures authority based control.
21. Dedicated air booster to avoid momentary pressure drop
22. One operator can easily operate two such machines (*)
(*) Arc plates are flat within 0.05, plating is uniform, and cutting burr is absent.
Features which can be added in standard machine
1. Automatic feeding of plates from vibro feeder to staking unit
2. Additional sensors to detect bent plate location
3. Additional station to sense plate missing assembly and eject it in rejection bin
4. Additional station for laser marking of each assembly with batch code for end to end traceability
5. Auto packing of output in boxes
6. Visual defect checking of output through camera system
Enamel Coating applicator for solar tank V1.0
Semi automatic, PLC Controlled
Suitable for 100 L to 500 L capacity of tanks
Easy to operate
Powder coated robust frame structure
possibility to convert to fully automatic operation with least harware changes

Enamel Coating applicator for solar tank V2.0
This coat applicator is our generation 2 SPM for automatically applying enamel coating on water tanks. only loading and unloading of tank is manual
Semi automatic, PLC Controlled
Suitable for 100 L to 500 L capacity of tanks
Easy to operate
Powder coated robust frame structure
possibility to convert to fully automatic operation with least harware changes

Enamel Coat Dryer
This SPM is needed for drying the excess water from the enamel coat before feeding the tank in side furnace
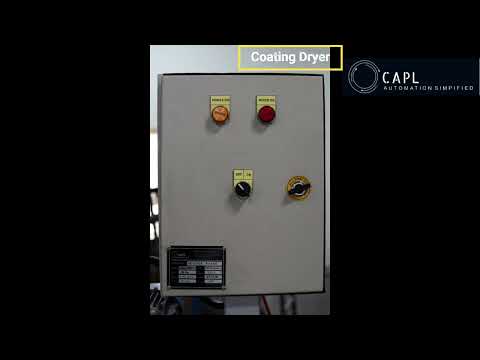
Solar Tank stand ( small C)
This SPM is made to cut and form a Small C. All the lengths can be made from same SPM jsut by select appropriate option from HMI
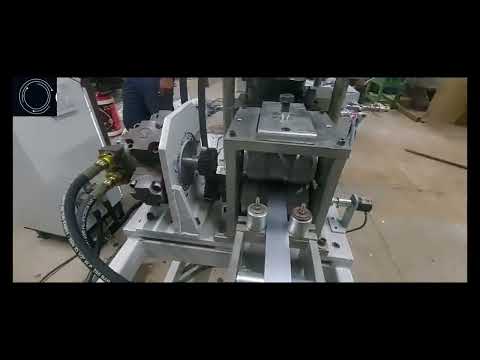
Solar Tank End flaring machine
This SPM is designed for flaring the end of solar water tank so that addtional step is created so that end cap can be fitted easility.
With this butt weld gets converted in to lap joint so that there is no weld penetration insdie tank

Semi -Automatic Shot Blasting for solar tanks
In solar tank manufacturing process, tank body must be cleaned from inside and prepared for better enamel adhesion.
Shot blasting soltion prepared by CAPL is one of our low cost soltion for serving this purpose. its designed to shot blast two tanks at a time and it is completely insulted thus do not cause any dust ontamination in the shopfloor.
its unique horzontal design allow easy loading and unloading and avoids digging of deep pits for its installation. PLC controlled shot blasting machine and user firndly HMI ensures operation of this machine by a low skilled operator.


Get in touch
Address
78/2 horamavu agara main road, Bangalore 560043, Karnataka, India
Contacts
91 8296999022
91 9819775122
Sales@contekautomation.com
Projects@contekautomation.com